Grooved Rolls
Unmatched Precision For Wire And Cable Straightening Rolls
The Highest Quality Grooved Rolls On The Market, For Any Application
Product Overview
Sjogren uses its engineering and machining expertise to create precision grooved rolls that fit any straightener assembly.
These rolls, with precision-cut grooves, cater to various needs. These include flat stock, bar stock, round and shaped wire and cables, including those used on oil and gas rigs. We also offer high-speed rolls to boost spindle uptime.
Sjogren's capabilities for innovative designs reduce disruptions, lower costs, and improve durability, making these grooved rolls the top choice in the market.
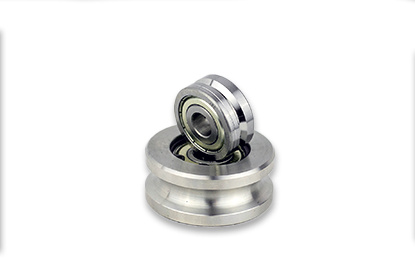
Key Benefits
Explore the essential features of our grooved rolls with our interactive model, or scroll down to access detailed technical specifications, including standard roll measurements and technical information.
1Completely Customizable
If your application calls for custom shaped wire, we can machine custom shaped grooves to match your specifications, even for small orders.
2Sjogren Alignment Marker
Exclusive to Sjogren Industries' rollers, the alignment marker ensures precise maintenance of the wire’s centerline from one roller to the next. While most grooved roll machining overlooks variations in bearing width, Sjogren employs precision measurement to pinpoint the exact groove position.
This alignment marker effectively addresses bearing width variations, simplifying the process for operators to correctly mount replacement rollers and uphold tolerances.
3Specialty Rollers
Working with precious metals, coated wire, or special shape wire and cable? We can help!
From custom u-grooves, square, star, cotter pin shapes, we have the precision to match your needs. We can also manufacture non-metallic straightener roll surfaces.
We design to fit your production.
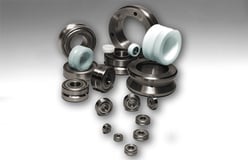
4Compatibility
Our grooved straightener rolls are compatible with any manufacturer’s assembly. Need replacements for a straightener we didn't make? Send us photos, specs, or a sample, and we will design for you.
5High-Speed Options
Sjogren's exclusive high-speed roller design enhances spindle uptime by facilitating increased line speeds and reducing the need for frequent replacements.
The High Speed Cartridge Assembly is adaptable to various straighteners and accommodates different roller sizes or groove shapes. This assembly features two pre-loaded bearings, ensuring exceptional straightener performance even at elevated line speeds.
These reduce roller wobble at high speed, which improves straightener performance.
The cartridge design stops over-tightening during replacement, removing a common mistake often made by less experienced operators.
Why Choose Sjogren's Grooved Rolls For Your Straightener?
Sjogren's precision and accuracy are unmatched in the industry.
-
1. Accuracy
- Sjogren's standard concentricity is .0005" (0,0127 mm), minimizing hairpin
-
2. Angle
- +/- .5° . (+/-30 min.)
- Precision. Is. Everything.
-
3. Centerline
- Parallel to edge within .0005"
-
4. Clean and Mean
- Rolls can be polished and stoned to perfection
Industries & Applications
Sjogren grooved rolls are trusted worldwide by manufacturers in almost any industry:

Industrial & Construction Manufacturing

Wire Processing & Wire Production

Energy & Power

Medical Wire Production
Our high-precision is essential to manufacturers of any medical wire application

Automotive

Mesh & Welding Manufacturing
Any Groove, Any Roller
Sjogren's precision and accuracy are unmatched in the industry. with standard concentricity of .0005" (0,0127 mm), the hairpin effect is minimized. Our centerline parallel edge is within .0005" (0,0127 mm). Here are a few common groove shapes as examples:

Vee Groove

Radius Groove

Hex Groove

Rectangle Groove

Flat Groove

Cotter Pin Groove
Product Measurements and Technical Specifications
Grooved Roll Technical Specifications - Metric
View Standard Metric-Roll Tech Specs
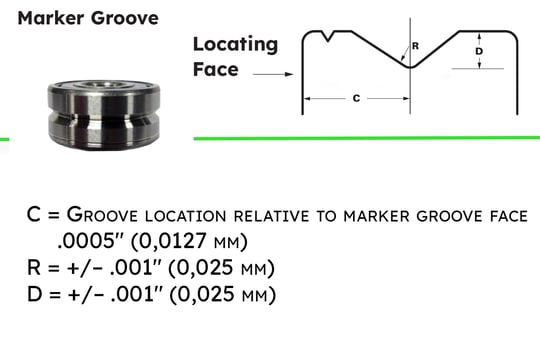
Part Number |
Model | Wire Diameter |
D | d | B |
---|---|---|---|---|---|
108066-01 | GR-07 | 0"-.008" 0-0,2 mm |
.276" 7 mm |
.118" 3 mm |
.118" 3 mm |
108066-03 | 683h-ZZ | .004"-.008" 0,1-0,2 mm |
.276" 7 mm |
.118" 3 mm |
.118" 3 mm |
108067-01 | GR10 | .0032"–.016" 0,08 mm–0,4 mm |
.394" 10 mm |
.118" 3 mm |
.157" 4 mm |
108152-05 | GR13 | .008"–.020" 0,2 mm–0,5 mm |
.512" 13 mm |
.157" 4 mm |
.197" 5 mm |
108018-02 | GR16 | .020"–.031" 0,5 mm–0,8 mm |
.630" 16 mm |
.157" 4 mm |
.197" 5 mm |
108080-26 | GR22 | 031"–.059" 0,8 mm–1,5 mm |
.866" 22 mm |
.315" 8 mm |
.276" 7 mm |
108080-67 | GR22 | .039"–.079" 1,0 mm–2,0 mm |
.866" 22 mm |
.315" 8 mm |
.276" 7 mm |
108168-01 | GR23 | .031"–.059" 0,8 mm–1,5 mm |
.906" 23 mm |
.315" 8 mm |
.276" 7 mm |
108168-07 | GR23 | .039"–.079" 1,0 mm–2,0 mm |
.906" 23 mm |
.315" 8 mm |
.276" 7 mm |
108181-00 | GR26 | .039"-.098" 1,0-2,5 mm |
1.024" 26 mm |
.315" 8 mm |
.276" 7 mm |
119623-00 | GR26-HSM2N | .039"-.098" 1,0-2,5 mm |
1.024" 26 mm |
.315" 8 mm |
.276" 7 mm |
108527-01 | GR30 | .059"–.118" 1,5 mm–3,0 mm |
1.181" 30 mm |
.394" 10 mm |
.563" 14.3 mm |
108191-03 | GR31 | .071"–.138" 1,8 mm–3,5 mm |
1.220" 31 mm |
.394" 10 mm |
.551" 14 mm |
108169-01 | GR32 | .059"-.157" 1,5-4,0 mm |
1.260" 32 mm |
.394" 10 mm |
.551" 14 mm |
108169-20 | GR32 | .079"–.157" 2,0 mm–4,0 mm |
1.260" 32 mm |
.394" 10 mm |
.551" 14 mm |
108128-12 | GR35 | .098"–.177" 2,5 mm–4,5 mm |
1.378" 35 mm |
.472" 12 mm |
.630" 16 mm |
108128-14 | GR35 | .079"-.177" 2,0-4,5 mm |
1.378" 35 mm |
.472" 12 mm |
.630" 16 mm |
108149-04 | GR40 | .118"–.197" 3,0 mm–5,0 mm |
1.575" 40 mm |
.591" 15 mm |
.630" 16 mm |
227662-01 | GR45 | .197"–.276" 5,0 mm–7,0 mm |
1.772" 45 mm |
.472" 12 mm |
.866" 22 mm |
108180-09 | GR47 | .157"-.315" 4,0-8,0 mm |
1.850" 47 mm |
.669" 17 mm |
.688" 17,5 mm |
227613-01 | GR52 | .276"–.354" 7,0 mm–9,0 mm |
2.047" 52 mm |
.472" 12 mm |
.827" 21 mm |
108607-02 | GR72 | .276"-.472" 7,0-12,0 mm |
2.835" 72 mm |
1.181" 30 mm |
.937" 23,8 mm |
227658-01 | GR80 | .315"–.591" 8,0 mm–15,0 mm |
3.150" 80 mm |
.984" 25 mm |
1.181" 30 mm |
Grooved Roll Technical Specifications - Inch Series
View Standard IS-Roll Tech Specs
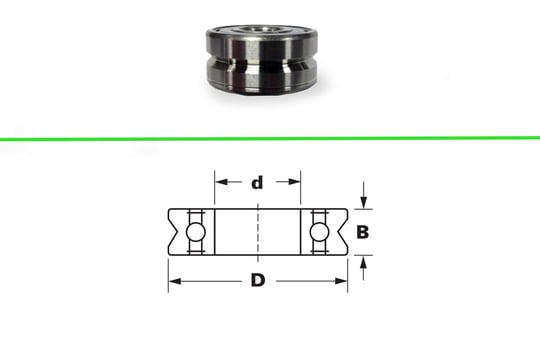
Part Number |
Model | Wire Diameter |
D | d | B |
---|---|---|---|---|---|
108535-04 | GR-S10-A | 0015"–.010" 0,038 mm–0,25 mm |
.1875" 4,76 mm |
.0937" 2,38 mm |
.0937" 2,38 mm |
108002-01 | SR144SS | 003"–.012" 0,076 mm–0,25 mm |
.250" 6,35 mm |
.125" 3,17 mm |
.1094" 2,79 mm |
108069-01 | R2ZZ | .003"–.015" 0,076 mm–0,38 mm |
.375" 9,52 mm |
.125" 3,17 mm |
.1562" 3,97 mm |
108070-01 | R3ZZ | .015"–.032" 0,38 mm–0,81 mm |
.500" 12,7 mm |
.1875" 4,76 mm |
.196" 4,99 mm |
108072-00 | R4AZZ | .030"–.062" 0,76 mm–1,57 mm |
.750" 19,05 mm |
.250" 6,35 mm |
.2812" 7,14 mm |
108087-01 | 5201ZZ | .062"–.125" 1,57 mm–3,17 mm |
1.259" 32,00 mm |
.472" 12,0 mm |
.625" 15,87 mm |
108093-01 | 5303ZZ | .125"–.250" 3,17 mm–6,35 mm |
1.850" 47,00 mm |
.669" 16,99 mm |
.875" 22,23 mm |
118653-01 | Tool Steel Sleeve |
.250"–.375" 6,35 mm–9,525 mm |
2.43" 61,98 mm |
.669" 16,99 mm |
1.05" 26,77 mm |
119415-01 | Tool Steel Sleeve |
.375"–.500" 9,52 5mm–12,7 mm |
3.25" 82,55 mm |
.787" 19,99 mm |
1.12" 28,57 mm |
Get the Application Data Sheet
Download the grooved roll application data sheet and share it with our team to get the right rolls moving for you with efficiency!
See some of our satisfied customers
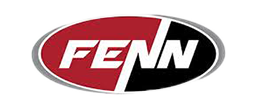
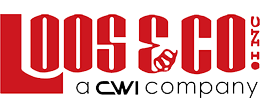
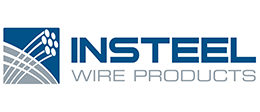
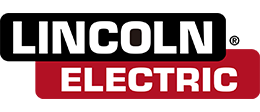
Grooved Roll FAQ
What is the difference that the alignment marker makes?
THE DIFFERENCE THAT SJOGREN’S ALIGNMENT MARKER MAKES:
A feature found only on Sjogren rollers, the alignment marker assures the operator that the wire’s centerline is maintained exactly from one roller to the next. The Sjogren alignment marker accounts for variations in bearing width and makes it easy for the operator to identify the correct way to mount replacement rollers to maintain tolerances.
The benefits include;
- Reduction in set-up time
- Vastly improves centerline alignment
- Improved productivity increases profits
How do you place the grooved roll with the orientation marker?
Review the following image for visual representation. you want the marker groove closest to the straightener base.
How do you set your grooved rolls on a straightener to eliminate curves?
Once you have mounted your rolls, you will adjust each knob slightly to slightly push the wire or rod down, and up respectively. Review the image below for a visual representation. the goal is to push just enough until the output is straight. This may take 2 or more planes, depending on your product.
What is the recommended maintenance schedule for grooved rolls?
The maintenance of your rolls is significantly influenced by their usage frequency, the surrounding environment, and the type of product being straightened. Below is a recommended maintenance schedule for vee and radius grooves, tailored for low, medium, high-carbon, and non-ferrous materials, based on 80-100 hours of machine operation.
Groove Type | Material | Replacement Frequency |
VEE | Low Carbon | 9 months |
VEE | Medium Carbon |
6 months |
VEE | High Carbon | 3 months |
VEE | Nonferrous | 12-18 months |
Radius | Low Carbon | 12 months |
Radius | Medium Carbon | 9 months |
Radius | High Carbon | 6 months |
Radius | Nonferrous | 15-21 months |
What do grooved rolls cost?
Our grooved rolls are engineered with precision, and our products stand out for their durability and quality.
Each application is custom to your application but its important to consider that pricing is swayed by volume. We provide volume pricing on all of our grooved rolls, no matter the shape of the cut, allowing you to benefit from cost efficiencies when ordering in bulk.
Our production process is optimized to reduce costs when manufacturing more units in a single run, and we share these savings with you.
Not ready to connect with us yet?
Dive deeper into our product lines and find the optimal solution for you, or dive into our news section to find the latest updates from how-to's to upcoming events and past.
Experience the Sjogren advantage—where simple ideas shape extraordinary solutions.
Sjogren News
See more of what Sjogren has to offer from educational content to the latest products and events. Subscribe to stay in-the-know!
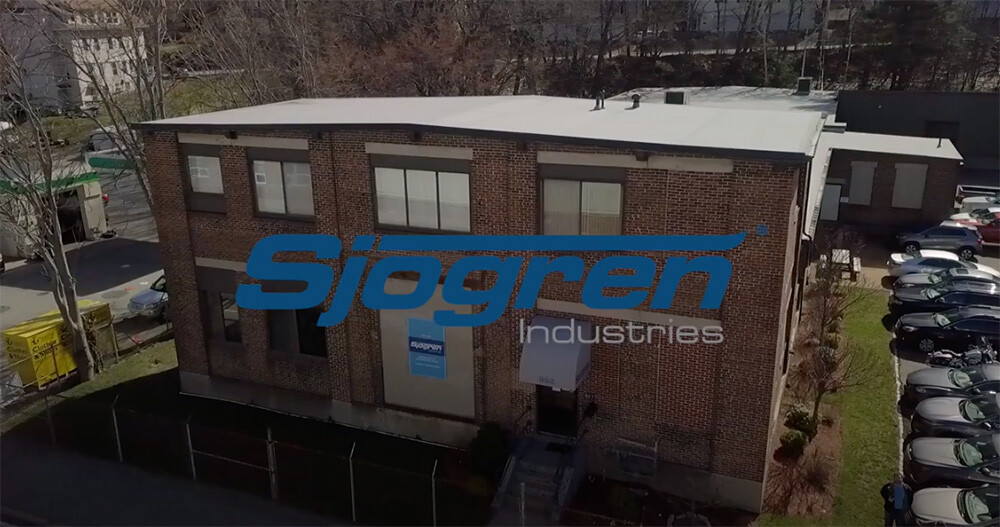
Product Lines
Head back to the product page to see more of Sjogren quality wire tooling
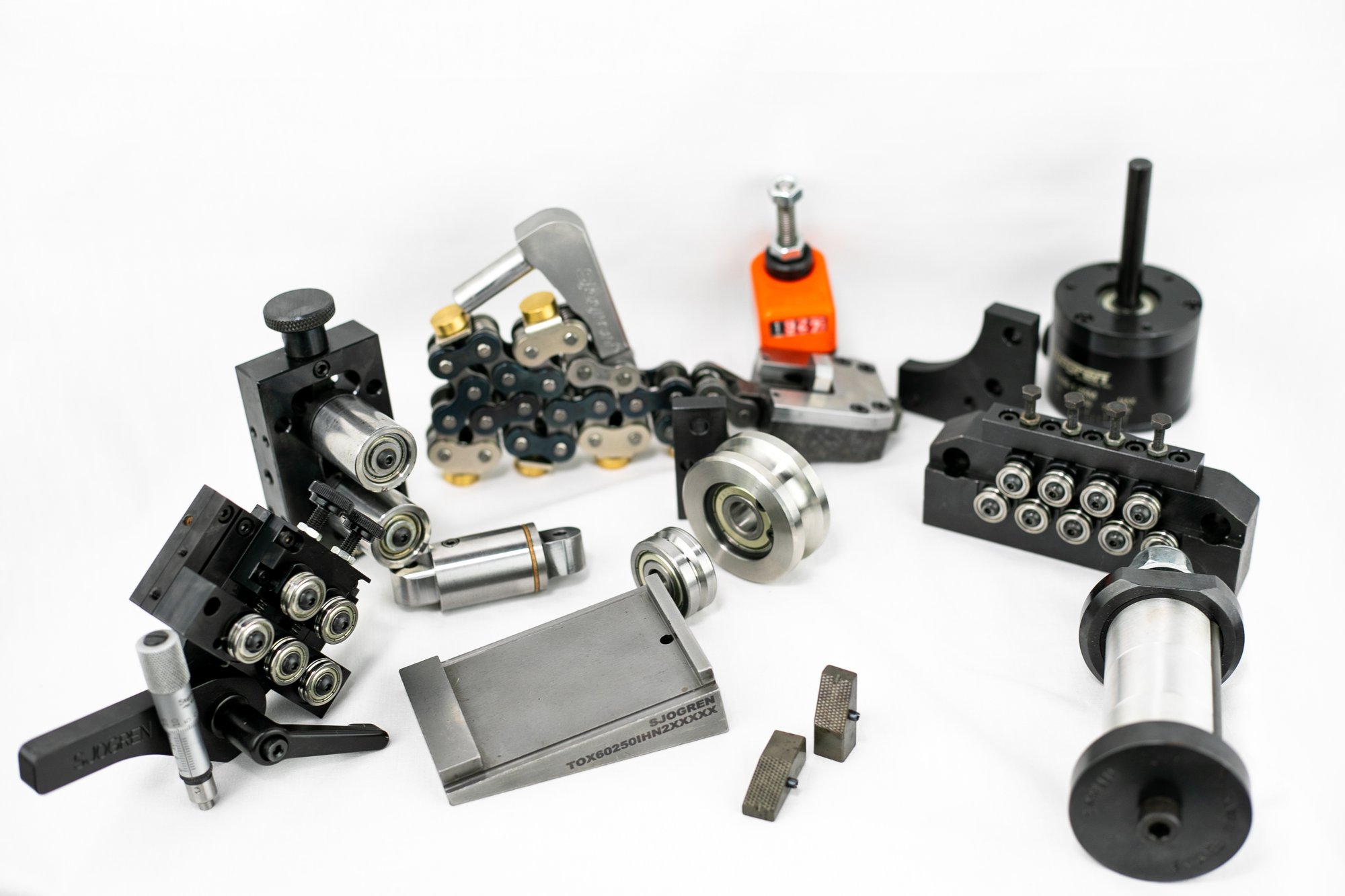
Product Lines
Head back to the product page to see more of Sjogren quality wire tooling
Sjogren News
See more of what Sjogren has to offer from educational content to the latest products and events. Subscribe to stay in-the-know!
Get Your Grooved Rolls Quoted – Fast & Reliable Pricing And Delivery!
Tell us your wire processing needs, and our team will provide a tailored quote quickly. Get the best solution for consistent wire drawing today!